Innowacyjna technologia wytwarzania ultra-wytrzymałych stali wykorzystywanych w przemyśle wydobywczym. Na pytanie odpowiada Rafał Zarzycki, prezes Zarządu, dyrektor generalny Gonar-Bis Sp. z o.o.
Biznes | Wydanie 160 | Gonar-Bis
Marka Gonar jest kojarzona z produkcją narzędzi dla przemysłu, ale prowadzicie także projekty badawczo rozwojowe. Niedawno sfinalizowaliście jeden z projektów realizowanych w ramach dofinansowania z Narodowego Centrum Badań i Rozwoju. Czego dotyczył ten projekt?
Gonar-Bis Sp. z o.o. w ramach Konsorcjum Naukowo-Przemysłowego wraz z Instytutem Metalurgii i Inżynierii Materiałowej PAN oraz Zachodniopomorskim Uniwersytetem Technologicznym w Szczecinie podjął się realizacji projektu pt. „Opracowanie i wdrożenie innowacyjnej technologii wytwarzania ultra-wytrzymałych stali przeznaczonych na strategiczne elementy maszyn w przemyśle wydobywczym”. Jako Gonar-Bis byliśmy liderem projektu.
Celem projektu było opracowanie i wdrożenie innowacyjnej technologii wytwarzania ultra-wytrzymałych stali wykorzystywanych w przemyśle wydobywczym. Zastosowanie nowych rozwiązań technologiczno-materiałowych umożliwiło otrzymanie elementów młotka dolnego o wyższych właściwościach mechanicznych, przy obniżeniu kosztów produkcji. Wartość projektu to prawie 31 mln zł, z czego wartość dofinansowania wyniosła ponad 16 mln zł.
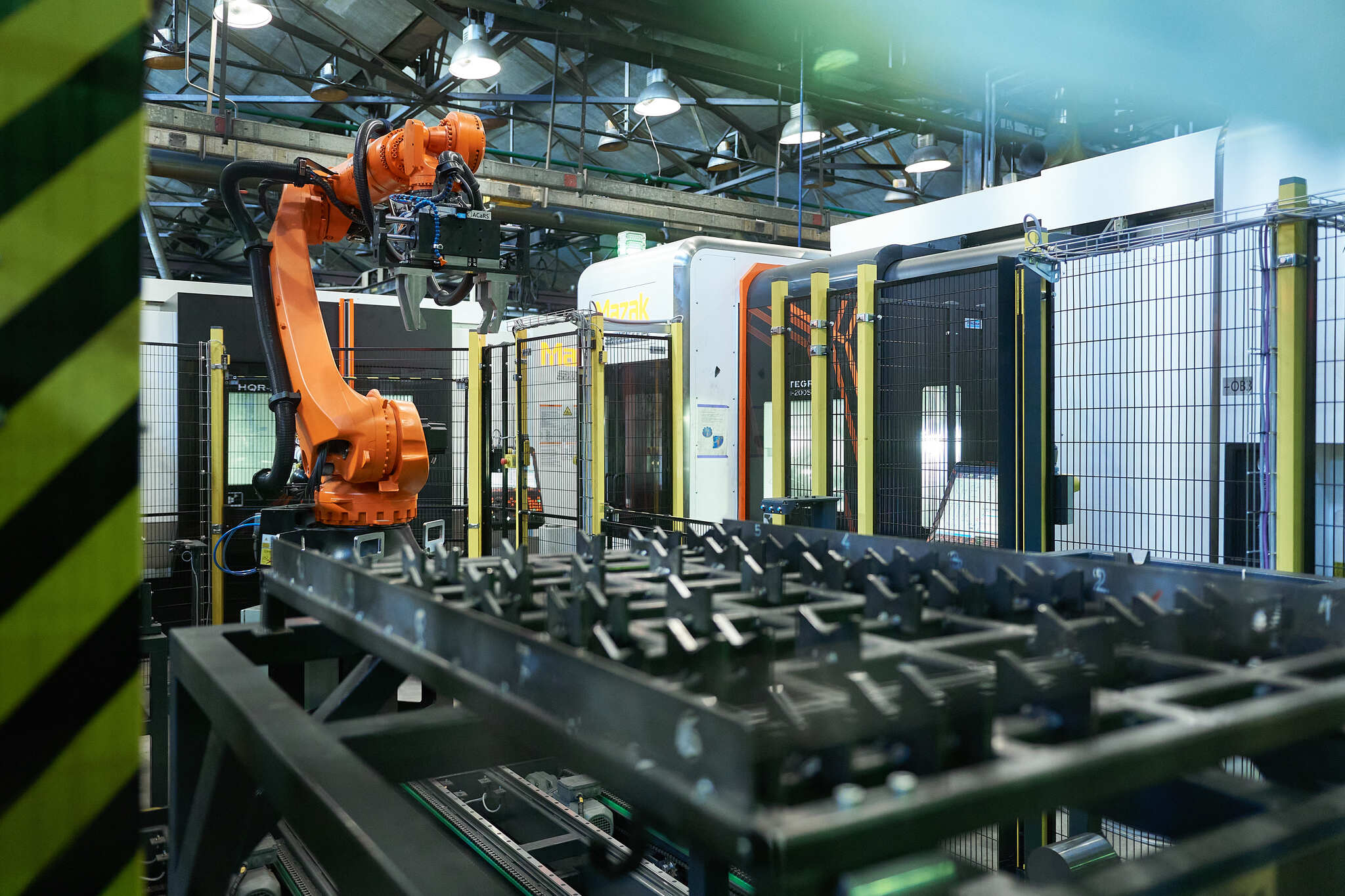
Czy może powiedzieć pan więcej o szczegółach projektu? Jaką rolę – prócz lidera projektu – pełnił w nim GONAR?
Projekt trwał od 1 stycznia 2020 do 30 czerwca 2024 roku. Każdy z członków konsorcjum miał inne zadanie: Instytut PAN był odpowiedzialny za dobór stali, Uniwersytet dopracował proces obróbki, tego materiału. Jako Gonar mieliśmy za zadanie stworzenie pilotażowej linii produkcyjnej, która była niezbędna do wykonania elementów narzędzi z badanego materiału, wyprodukowanie ich oraz testy.
Dzisiaj, po zakończeniu projektu, możemy z całą pewnością stwierdzić, że testy wypadły bardzo pozytywnie – klienci, którzy sprawdzali narzędzia z elementami z ultra-stali są z nich bardzo zadowoleni i już teraz składają zamówienia.
Projekt pozwolił na wzrost wydajności procesów produkcyjnych – m.in. dzięki zastosowaniu nowych materiałów narzędziowych oraz wysokich parametrów użytkowych maszyn. Dzięki pilotażowej linii produkcyjnej zoptymalizowano sam proces, co przełożyło się też na zmniejszenie zużycia energii elektrycznej o 20 procent. Dzięki wykorzystaniu nowej stali obniżono wagę konstrukcji młotka dolnego. Przede wszystkim jednak osiągnięto cel nadrzędny, jakim było zwiększenie trwałości narzędzi.
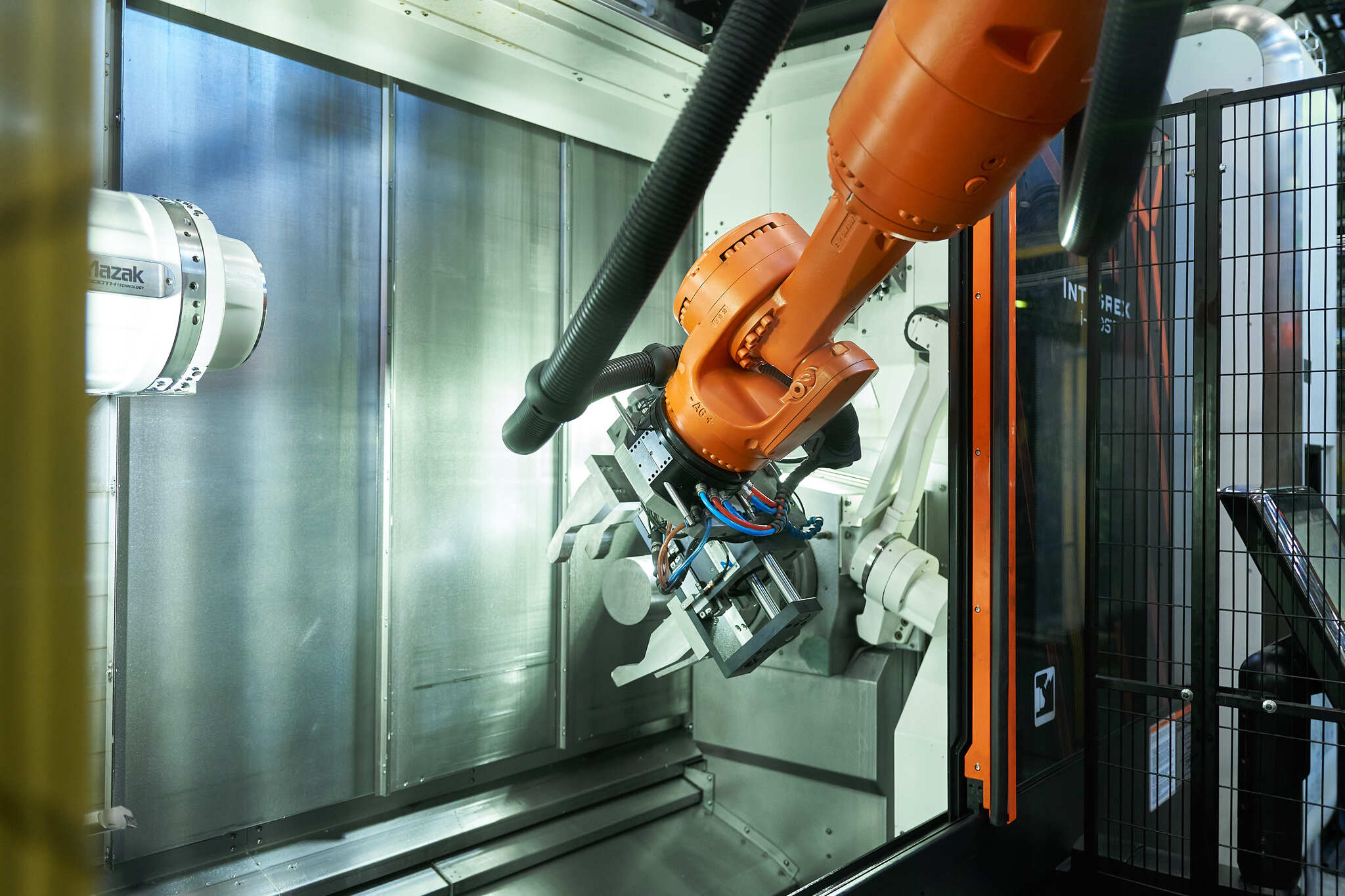
Co wpłynęło na sukces projektu?
Na pewno doświadczenie wszystkich członków konsorcjum. Jako Gonar wykorzystaliśmy swoje niemal 50-letnie doświadczenie w tworzeniu narzędzi. W fazie projektowej zoptymalizowaliśmy kształty elementów młotka tak, by jak najlepiej wykorzystywały właściwości nowej stali i dzięki temu udało się uzyskać narzędzia o lepszej wytrzymałości i bardzo dużej precyzji.
Instytut Metalurgii w Krakowie to uznana jednostka naukowa zajmująca się stalą, a naukowcy z Uniwersytetu Zachodniopomorskiego nie tylko mają doświadczenie związane z badaniami nad stalą, ale także mają ogromne zaplecze laboratoryjne i mają ogromną wiedzę związaną z obróbką stali.
Ważne dla nas było połączenie tych elementów: rodzaj stali, proces obróbki i nowoczesna linia produkcyjna. Skład chemiczny stali ma fundamentalne znaczenie dla jej własności mechanicznych – ale bez odpowiedniej obróbki również nie osiągniemy pożądanego efektu. Tylko synergia tych elementów mogła pomóc w realizacji tego projektu.
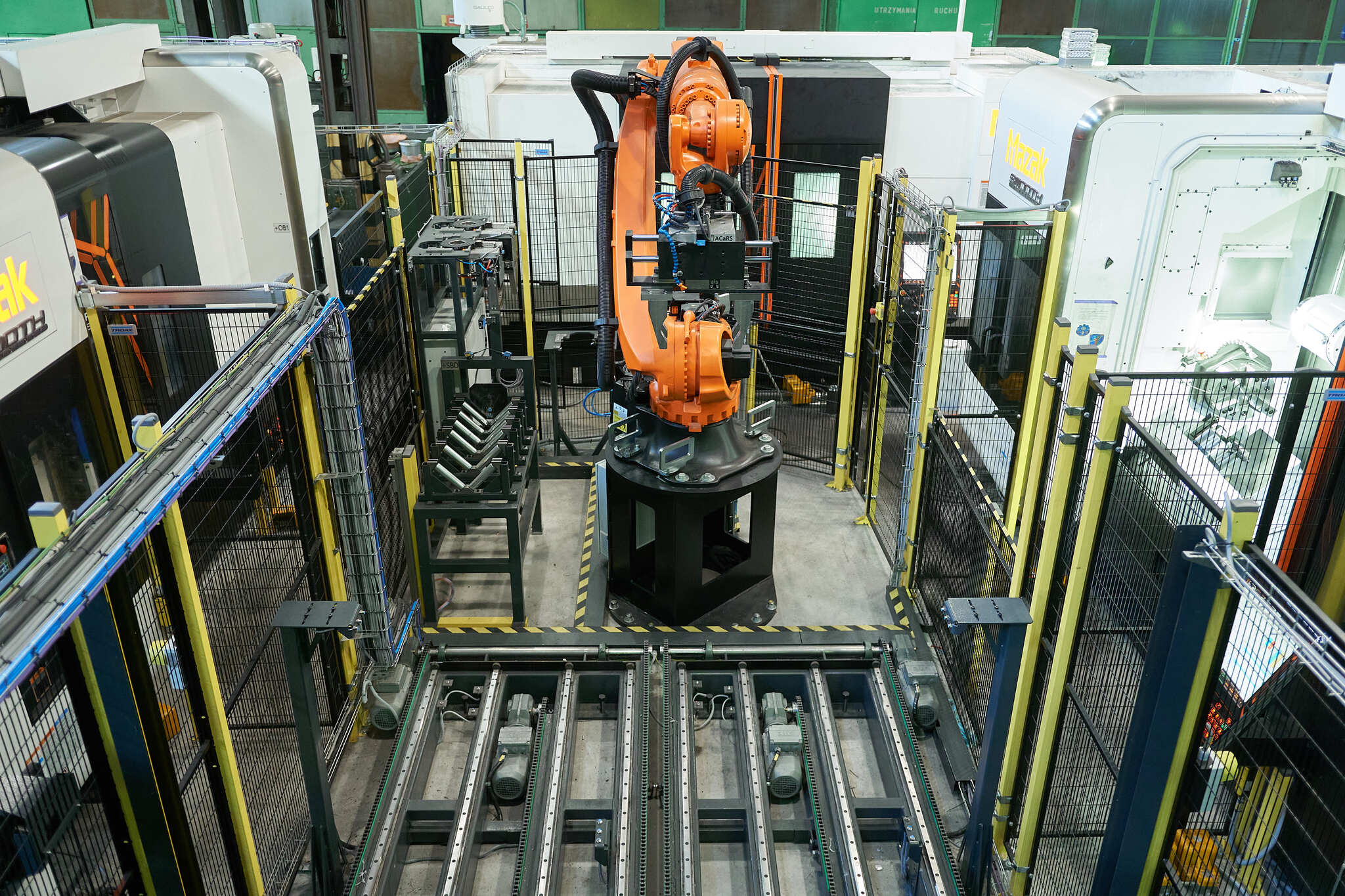
Jakie trudności napotkaliście w trakcie realizacji zadania?
Cele założone w projekcie zostały zrealizowane, ale nie było to takie proste, jak się teraz wydaje – np. wytypowaliśmy kilka rodzajów stali, zanim znaleźliśmy taki, który odpowiadał nam pod względem właściwości mechanicznych.
Dużym wyzwaniem było skoordynowanie wszystkich podwykonawców maszyn i urządzeń tak, abyśmy mogli zrealizować projekt. Co więcej, w projekt jest wpisana komercjalizacja, co znaczy, że badania nad procesem produkcyjnym musiały okazać się opłacalne – to ważne, bo w wielu projektach badacze zapominają zupełnie o elemencie opłacalności technologii.
A trzeba pamiętać, że opracowanie nowego produktu to jedno, a przekonanie klientów – to drugie.